Core competence in development, design and production
Highest quality is created with passion. A passion that is realised through deep technical expertise and state-of-the-art instruments and processes. At the Harmonic Drive SE headquarters, all these factors come together and form the foundation of decades of technological leadership in the field of high precision drive technology.
Investing in the future
In addition to the wholly-owned subsidiaries throughout Europe, Harmonic Drive SE made a sustainable investment in the future as early as 2006: the company built a development centre which, with an area of 2400 m², still offers the best conditions for any development activities today.
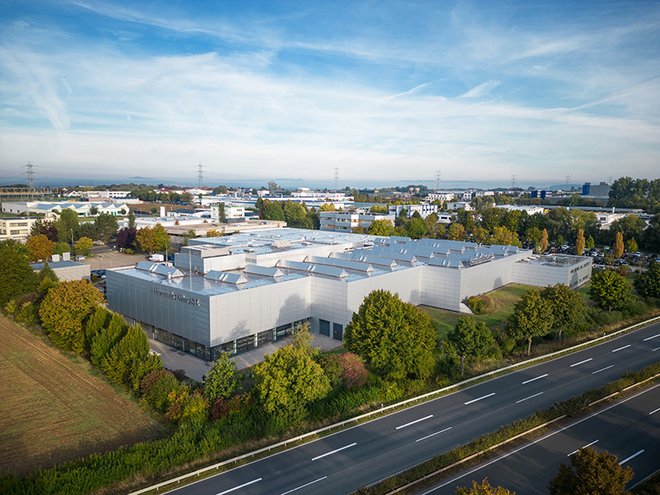
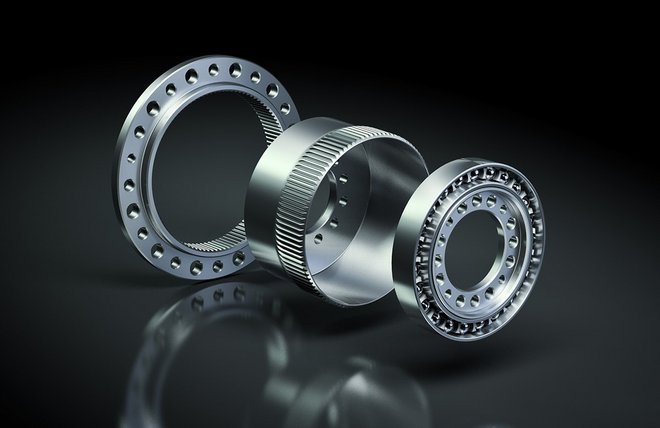
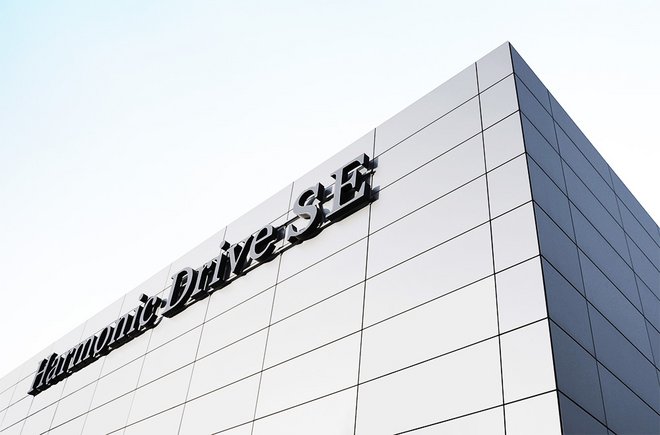
Expertise on site – the Harmonic Drive® cevelopment centre
What we know, is the configuration of adequate components is complex. This makes the cooperative development of a complete solution proposal for the drive task to be realised all the more important. Starting with the selection of suitable gearboxes and the matching motor and sensor components, we configure the complete drive axis for your application.
In doing so, we look back on decades of experience. Since 1970, we have been building on a multitude of realised complex drive solutions, giving our customers a technological edge. All design elements can be customised and optimally matched to each other. Integration into the application always takes place in close cooperation with our customers. The decisive factors here are, on the one hand, the high flexibility and, on the other hand, the individual scope of services and integration level. The result: an optimal overall solution for your application.
In our modern development centre, a team of more than 40 designers and engineers is available every day. Up-to-date design and calculation tools, self-designed tools for fast analytical calculations and equally established FEM-supported methods are used. In the directly connected test field, the newly developed actuators and drive systems are verified for performance and functionality with the help of specific test benches. The knowledge gained from this is fed back into development and forms the basis for further optimisation.
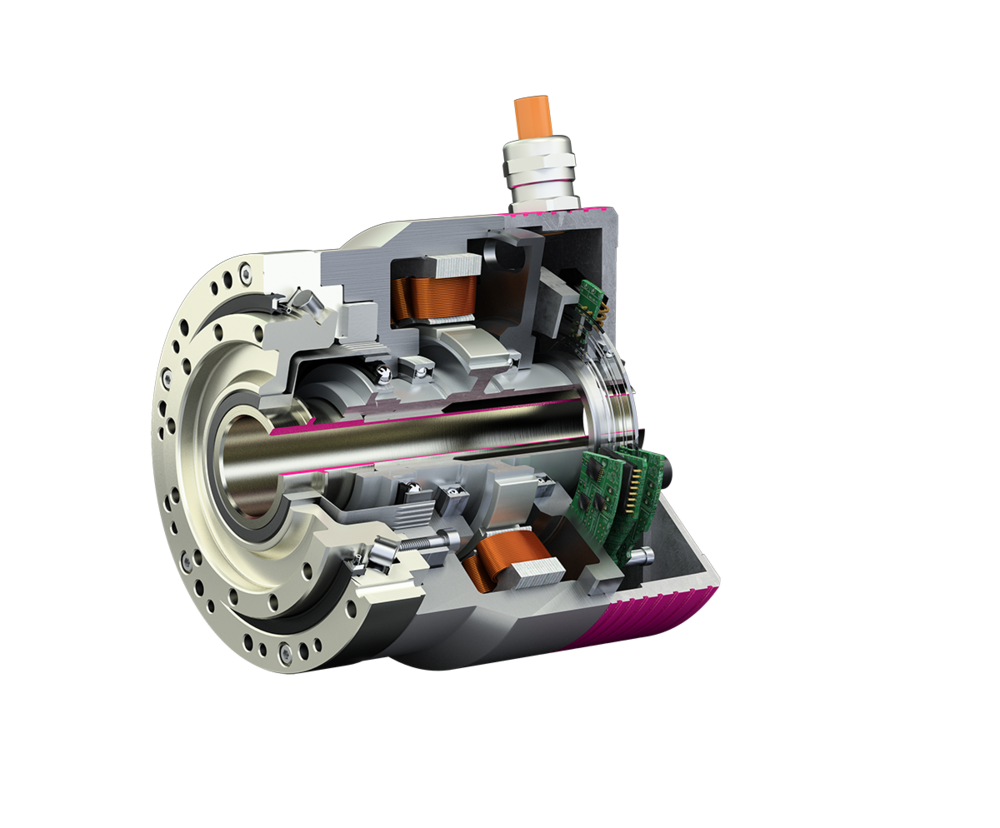
Increase in production capacities
The course for an increase in productivity was set in 2013 by a plant expansion and the installation of new production lines at the company's main location in Limburg an der Lahn in Germany. In addition to profitable effects and the additional space expansion totaling 6,500 m², which also accommodated a measurement laboratory, the plant expansion offered further advantages. Flexible operating media supply for machines and lines, constant air conditioning with active air dehumidification, 30 % electricity savings through lighting with LED technology, high maximum floor load capacity and barrier-free access made the factory expansion another investment for the future.
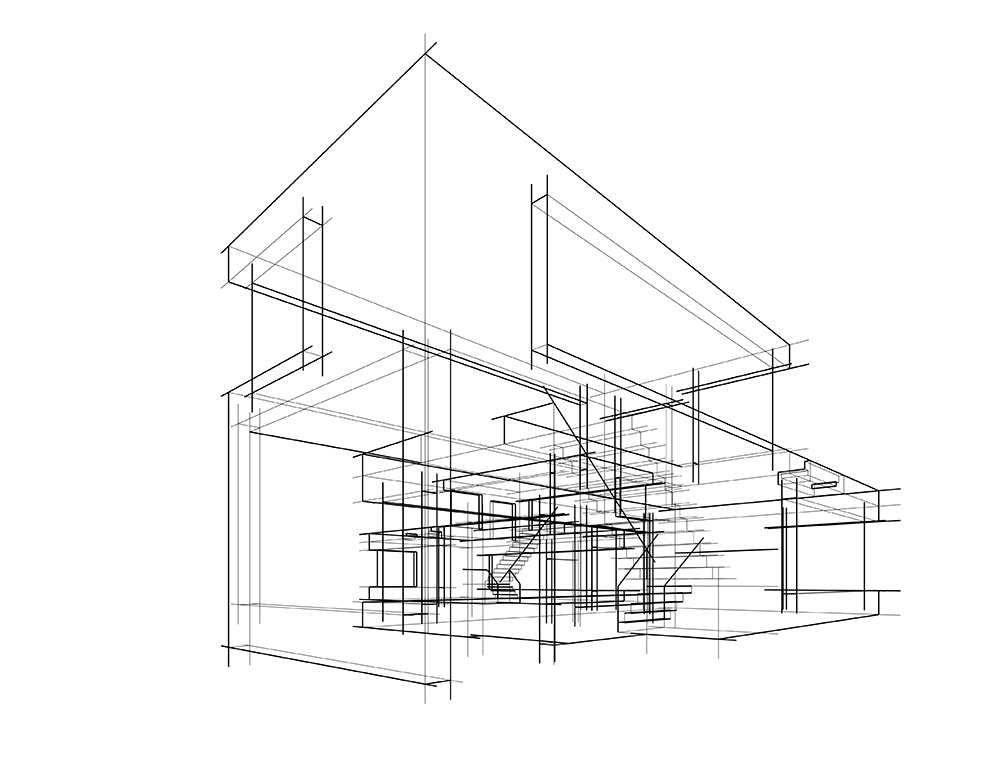
Local component production
In 2017, Harmonic Drive SE invested in a further production site not far from the main site in Limburg an der Lahn in order to meet the continuing growth and turnover impulses, to be able to guarantee increased incoming orders and to prevent production bottlenecks. The previous 20,400 m² of space was thus expanded by 1,600 m². In addition to increasing production capacity, the second Limburg site also serves to optimise process flows and focuses, in particular, on the production of crossed roller bearings, which, as high precision bearings, enable maximum load capacity in the smallest volume and are a component of Harmonic Drive® Gears.
Equipped in time - from batch size 1
In addition to a few standard products with higher quantities, our production is dominated by many variants and the most diverse assemblies in smaller quantities starting from batch size 1. This is because almost all products that leave our premises are configured together with you, according to your specific wishes and requirements and then manufactured in-house. In order to achieve this high flexibility in production, we have developed an intelligent set-up concept with which we can even manufacture batch size 1 economically.
Production lines per size enable us to change set up smoothly and thus ensure maximum flexibility - even for small batch sizes. In order to meet these requirements throughout the entire value chain, we rely on long term supplier relationships based on partnership in the area of supply chain management, which we continuously develop into efficient supplier structures and thus synchronously align with our production system. In this way, we fulfil your wishes individually, no matter what the quantity.
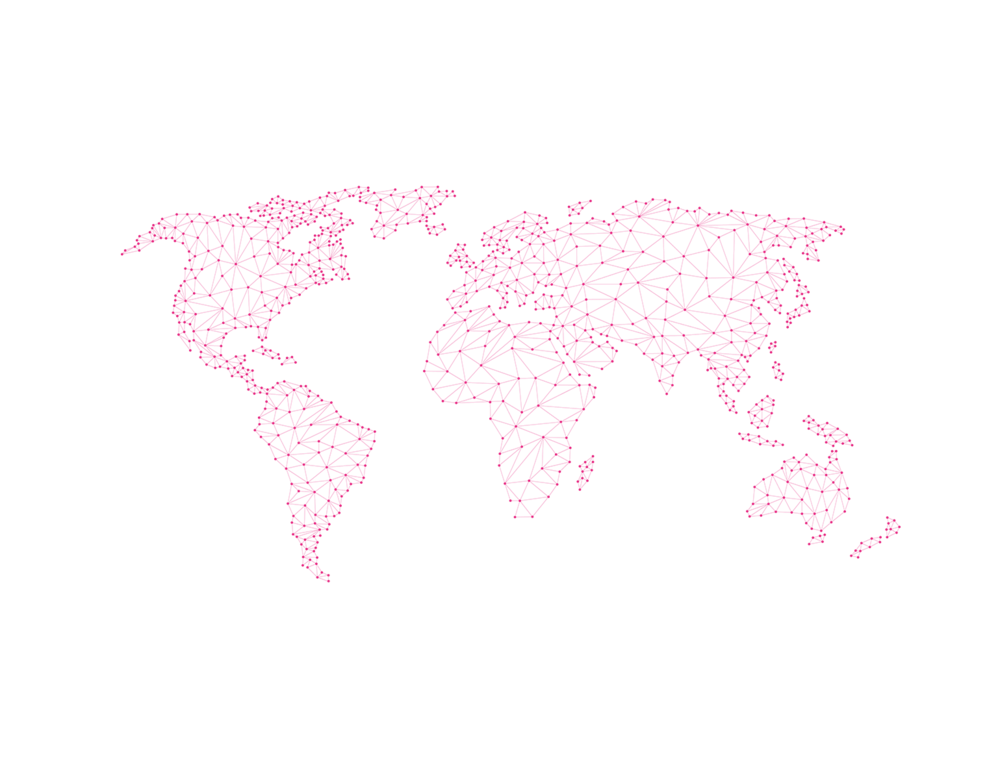
Harmonic Drive® worldwide
Through our worldwide locations and close cooperation with our parent company in Japan as well as our sister companies in the USA and China, we ensure that you benefit from customised drive solutions of the Harmonic Drive® brand around the globe - we are there where you need us. In doing so, we do not only overcome country and date borders, we also find the right answer for your complex questions.
Technology leader and partner
Working successfully with, and for, our customers in demanding industries and applications is a sign of innovative strength in the field of high precision drive technology. Harmonic Drive SE has established itself as a technology leader over the years. Thanks to continuous production and process optimisations, unrestrained development power and in-depth technical expertise, it stands by its customers as a loyal partner.
-
0Employees
-
0sqm area
-
0Years of expertise
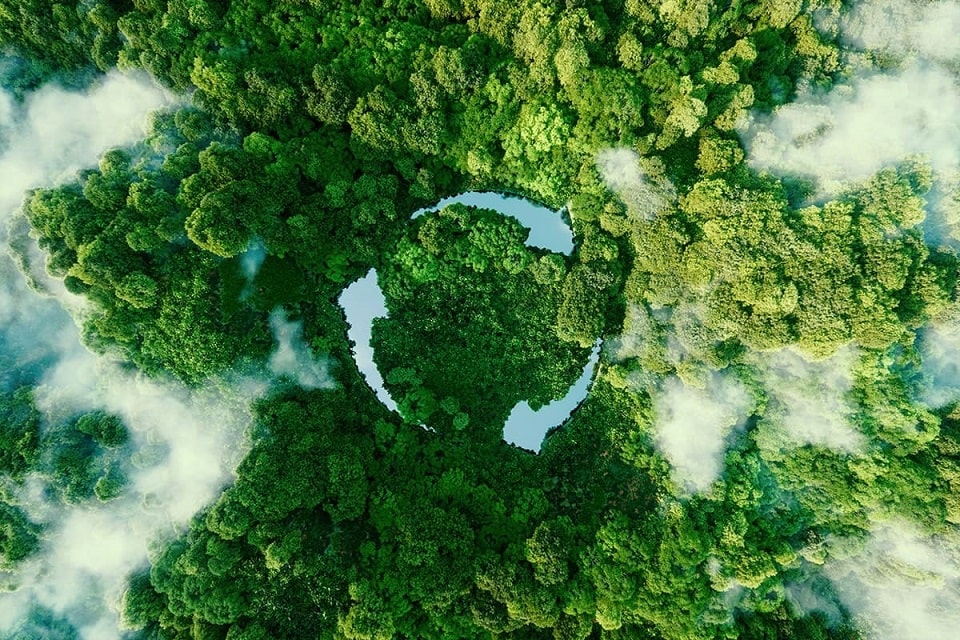
Sustainable production
In spring 2022, Harmonic Drive SE introduced an energy management system in accordance with the DIN EN ISO 50001:2018 standard. This continuously increases energy efficiency in the company and sustainably reduces energy consumption and greenhouse gas emissions. With the help of energy management, the energy flows in the company and the associated energy sources are recorded, analysed and potential savings identified.
However, the focus on fair and sustainable production conditions began years earlier. In the course of the plant expansion in 2013, the use of geothermal energy (geothermal heat) for heating and cooling our buildings was implemented early and consciously - also to ensure a constant temperature and humidity to safeguard our production quality. Alternative forms of energy are an integral part of the quality, sustainability and ecology guidelines as well as the company's environmental and energy policy guidelines.
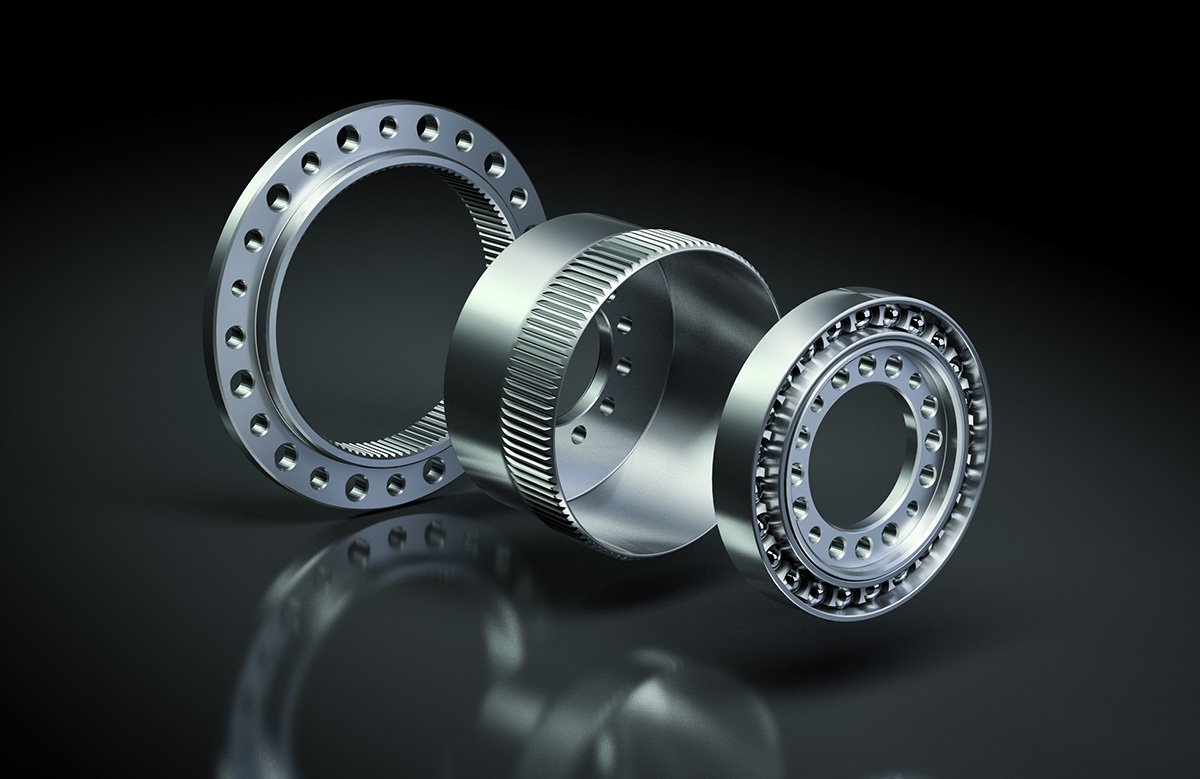
The secret of the Harmonic Drive® Gear
It is no longer possible to imagine drive technology without the strain wave gear. Its special features and characteristics explained in detail.
View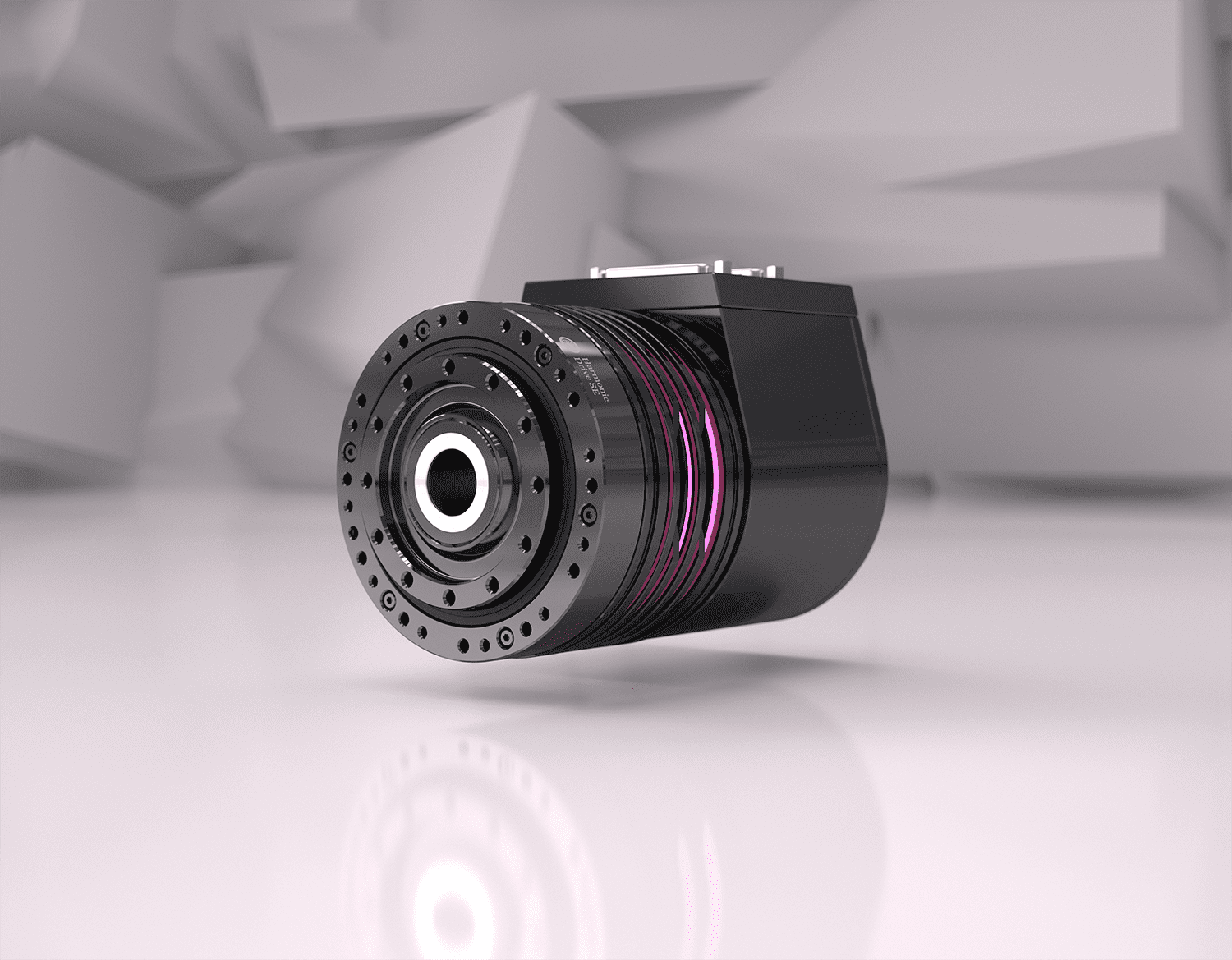
Smart System IHD: Pioneering drive technology
The need for compactness and intelligence is growing – especially in industrial and mobile drive technology.
View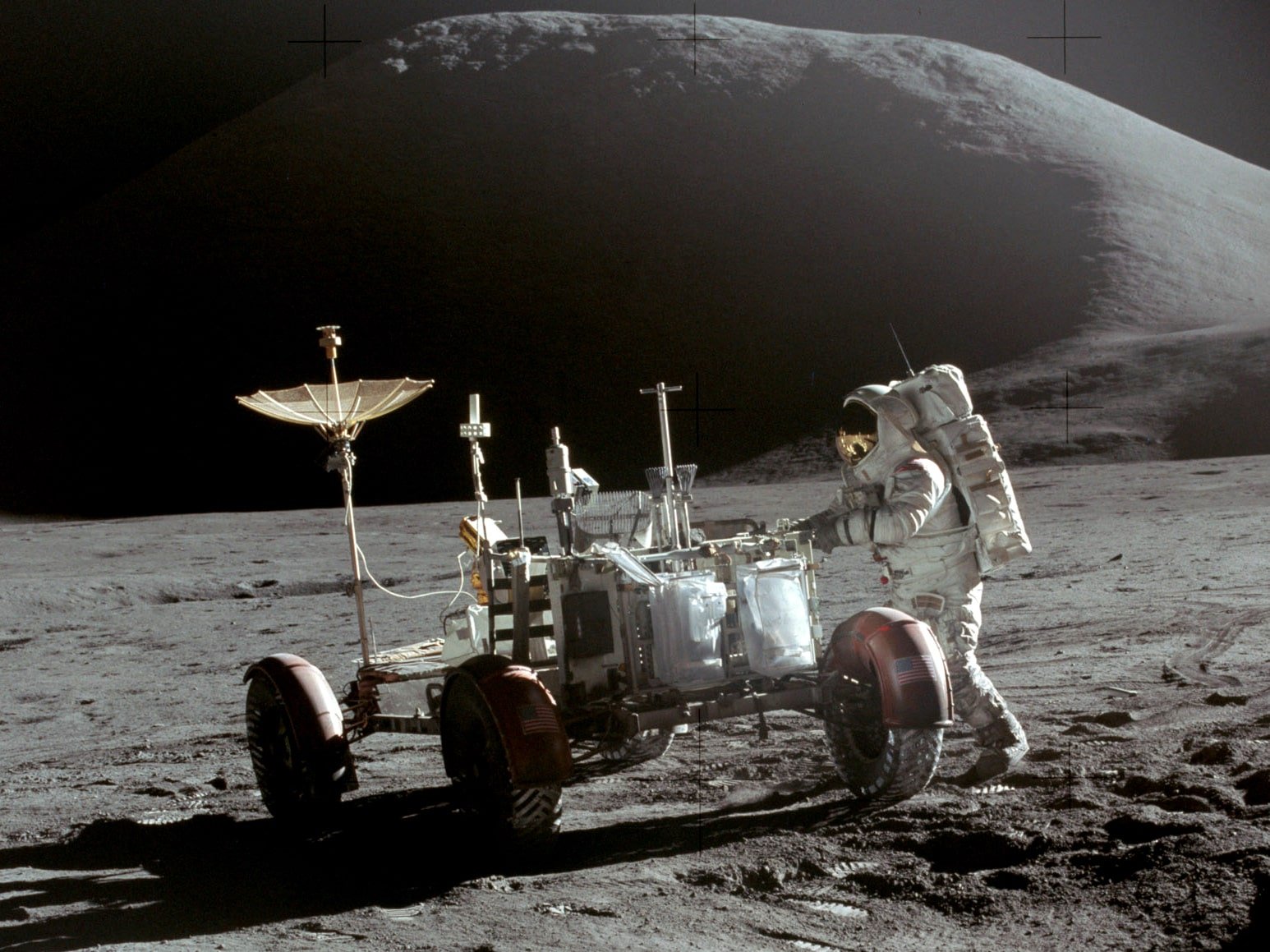
Mission Apollo 15 – Harmonic Drive® on the Moon
The year is 1971. On 26 July, Apollo 15 sets off for the moon from the Kennedy Space Center in Florida.
View