The secret of the strain wave gear
Harmonic Drive® Gears have flown to the moon and Mars, are installed in the most modern robotic applications in the world and established themselves decades ago as an integral part of future-oriented drive technology. All this is made possible by one thing: the unique functional principle.
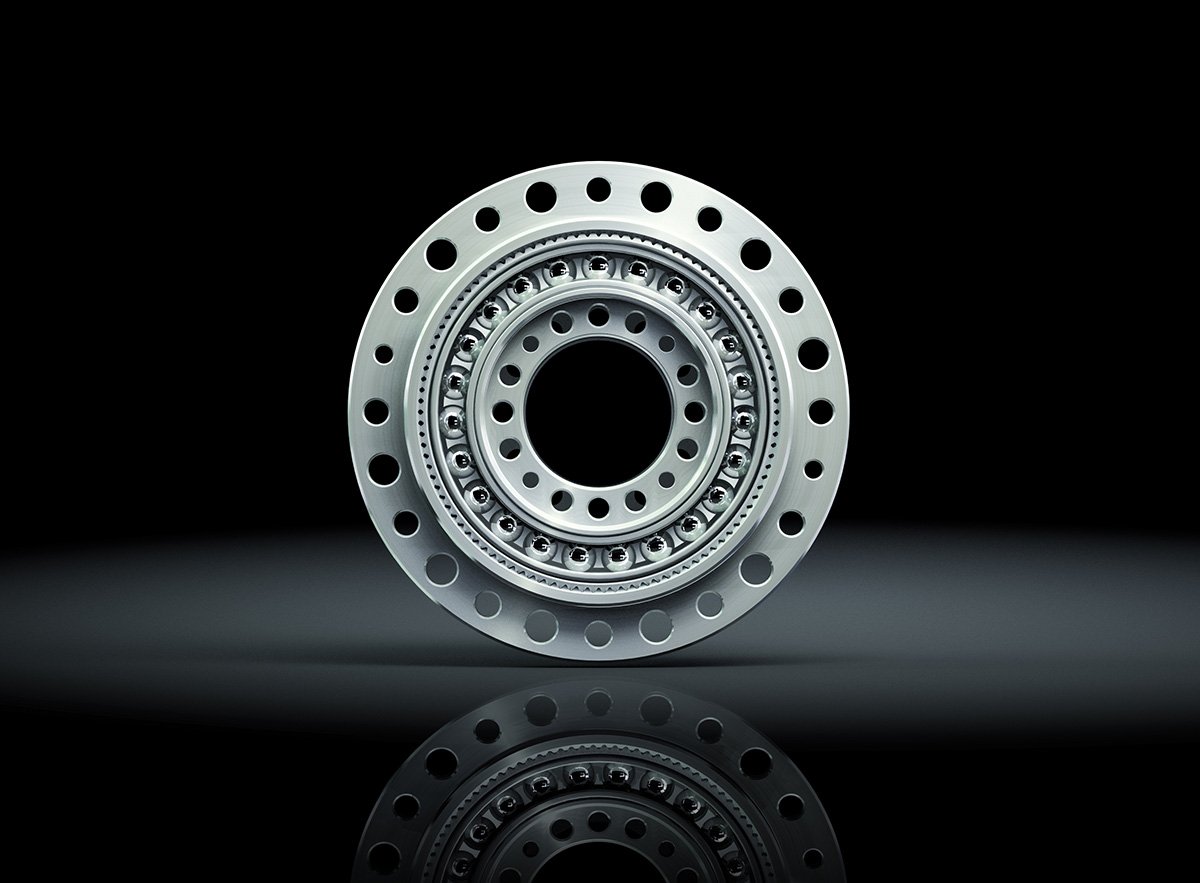
How it all started
The invention of the strain wave gear dates back more than 60 years. Even today, the principle and aesthetics of the gear inspire developers, designers and technology enthusiasts around the globe. Responsible for this: the creativity of one man – Clarence Walton Musser.
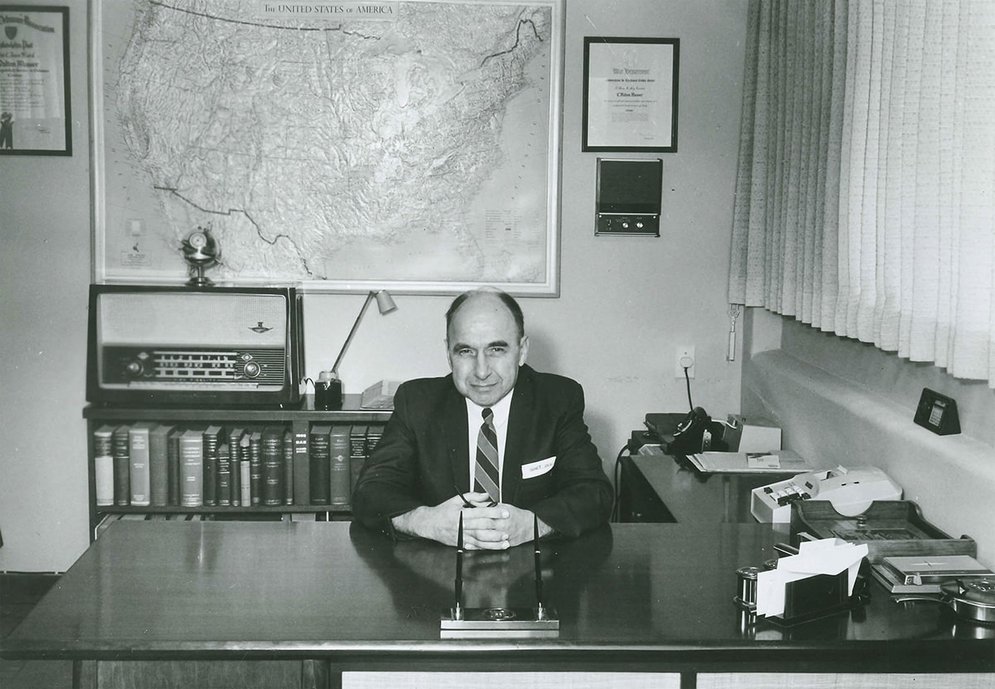
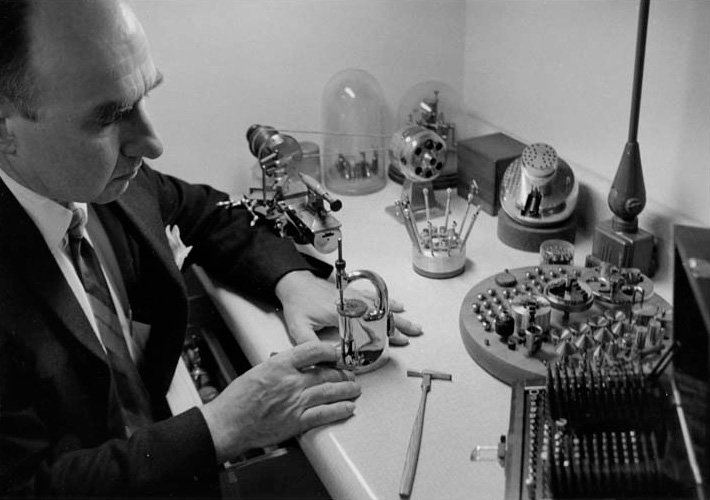
The man behind the gear
Clarence Walton Musser was a contemporary man who incorporated both the past and the future into his thinking and inventive ways. His genius and technical understanding resulted in well over 200 patents that were not concentrated or even limited to Musser's special field, mechanical engineering. Whether in the areas of physics, chemistry or biology - the US-American distinguished himself through his wide-ranging interests, with his completely restless mind and analytical abilities.
Equal to Musser's patriotism were ethics and honesty. His intellectual abilities were as legendary as his sense of humour - and so a day with Walt, as friends and acquaintances called him, was always like an adventure. To recognise his genius, it was enough to listen to him. Equally strong in character was his choice of friends. He avoided aloof people and rather had close contact with those he truly liked, regardless of their position in society.
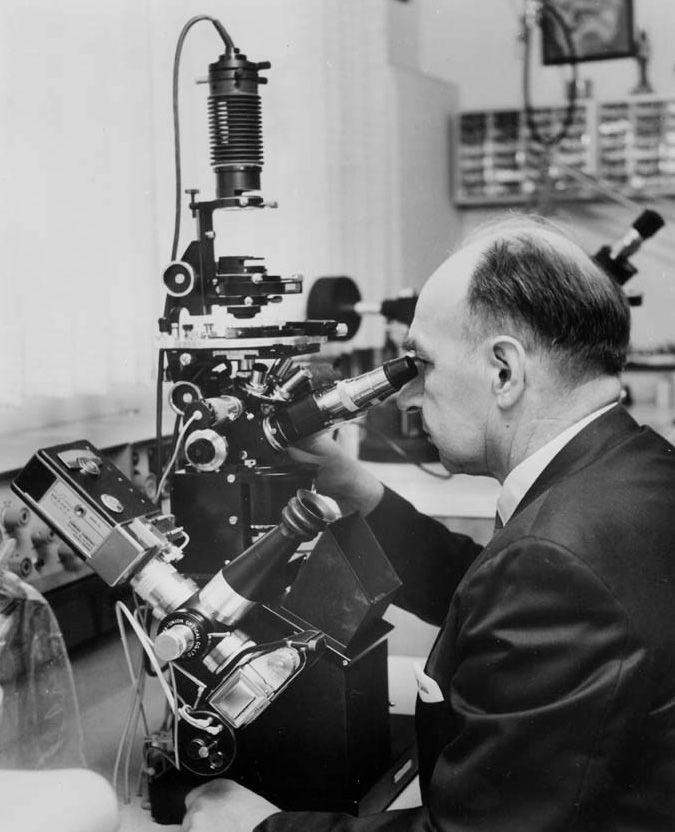
Engineer & pioneer
Born in Lancaster, Pennsylvania in 1909, Musser attended Chicago Technical College, the University of Pennsylvania and the Massachusetts Institute of Technology after graduating from high school. While still operating his engineering firm, which opened in 1935, Musser worked as a consultant for the United States government and various companies, including General Motors, Olin Mathieson and the United Shoe Machinery Corporation.
Musser received the Exceptional Civilian Service Award for his research consulting at the Frankford Arsenal, a development centre of the United States Army, and the design of recoilless guns. He was also honoured by the American Society of Mechanical Engineers.
Clarence Walton Musser was to have succeeded in 1955 with the one invention that would continue to set our planet in motion in a wide variety of applications for decades to come: the strain wave gear.
"It is never a question as to whether it can be done – it is only whether one cares to spend the time and effort."
Elastic bodies made success possible
After Musser had devoted himself to aviation in the late 1940s and early 1950s, which resulted in the invention of the ejection seat and the canopy for jet aircraft, among other things, his attention fell on elastic bodies. So he then began his study and research in this field and, in doing so, he sometimes relied on controlled bending and deflection. Later, he applied these to new mechanical designs, structures and concepts - and finally developed the functional principle of the strain wave gear.
Even today, the features of Harmonic Drive® Gears presented above are largely based on the interaction of their simple design, but above all on the unique principle of elastic deformation of gears and the Flexspline respectively. The latter is a high strength, torsionally stiff, yet flexible component that reliably transmits high loads.
Constancy and adaptability
Whether in a housing, as an actuator with motor and encoder or as part of customised configurations, adaptability of the Harmonic Drive® Gear enables a wide range of applications. However, the functional principle itself has remained constant over all these years.
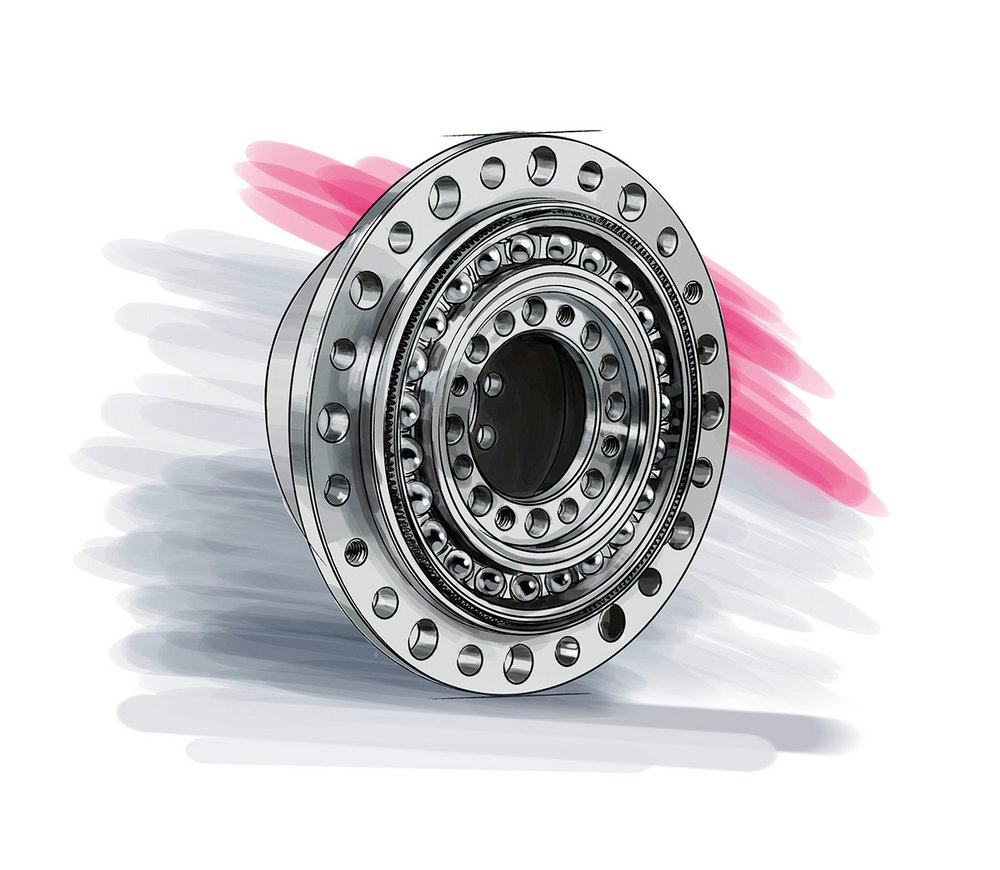
Key features
- Due to high reduction ratios with only three basic components and coaxial alignment, strain wave gears can be easily integrated into existing applications.
- Small dimensions and low weight compared to conventional gear types allow the use in compact and lightweight applications.
- Harmonic Drive® Gears exhibit absolute zero backlash throughout their service life and maintain high torsional stiffness over the entire torque range.
Functional principle explained
The Harmonic Drive® Gear is based on three components. The basis is embodied by the Wave Generator, an elliptical steel disc at the heart of the gear. It has a centric hub and a thin, elliptically deformable special ball bearing. The Wave Generator uses the ball bearing to deform the Flexspline, a deformable cylindrical steel sleeve with teeth arranged radially around the outside. As a rigid and cylindrical outer ring, it is the Circular Spline, which is the third component surrounding both Wave Generator and Flexspline and is equipped with internal teeth.
As the Wave Generator rotates, the large elliptical axis shifts and with it the gear meshing area. The number of teeth themselves is of great importance - the external teeth of the Flexspline have exactly 2 teeth less than the internal teeth of the Circular Spline. Accordingly, during a half rotation of the elliptical Wave Generator, there is a relative movement of one tooth between the Flexspline and the Circular Spline; during a full rotation, there are already two teeth.
Outstanding features
The fact that Harmonic Drive® Gears are used in such a diverse range of sectors, industries and applications is due to their wide-ranging performance characteristics. These include the following:
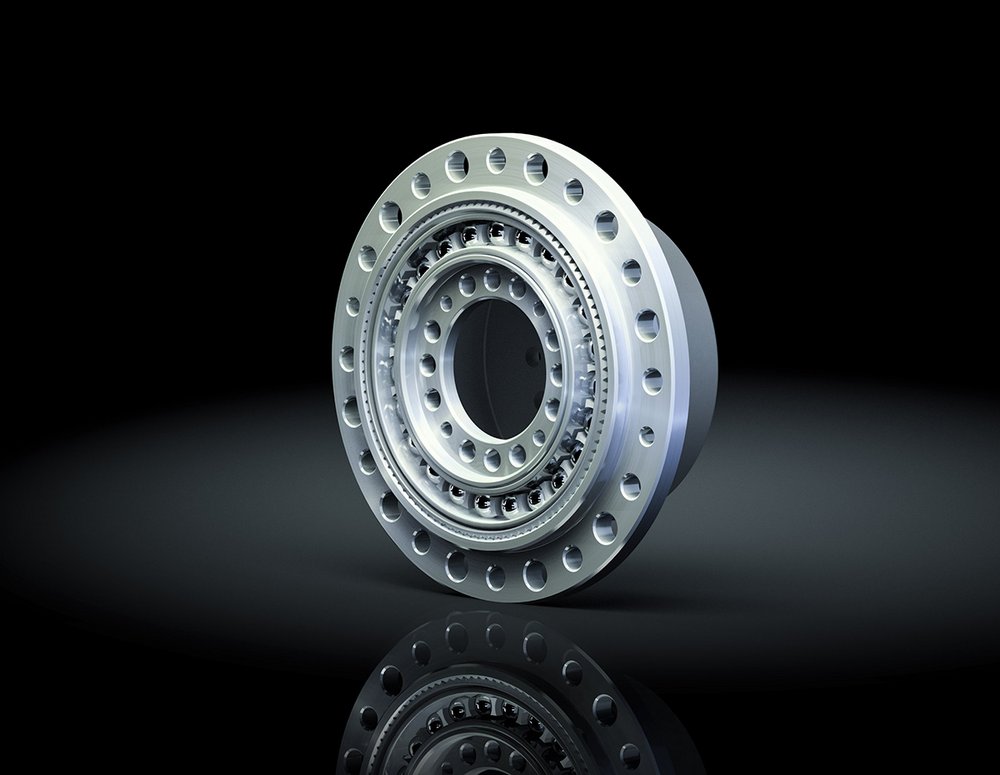
Absolute freedom from backlash
Harmonic Drive® Gears show no backlash increase in the teeth over their entire service life.
Positioning and repeatability accuracy
Harmonic Drive® Gears have an excellent positioning accuracy of less than one angular minute and a repeatability of only a few angular seconds.
Small dimensions and low weight
Harmonic Drive® Gears are much more compact and lighter than conventional gears.
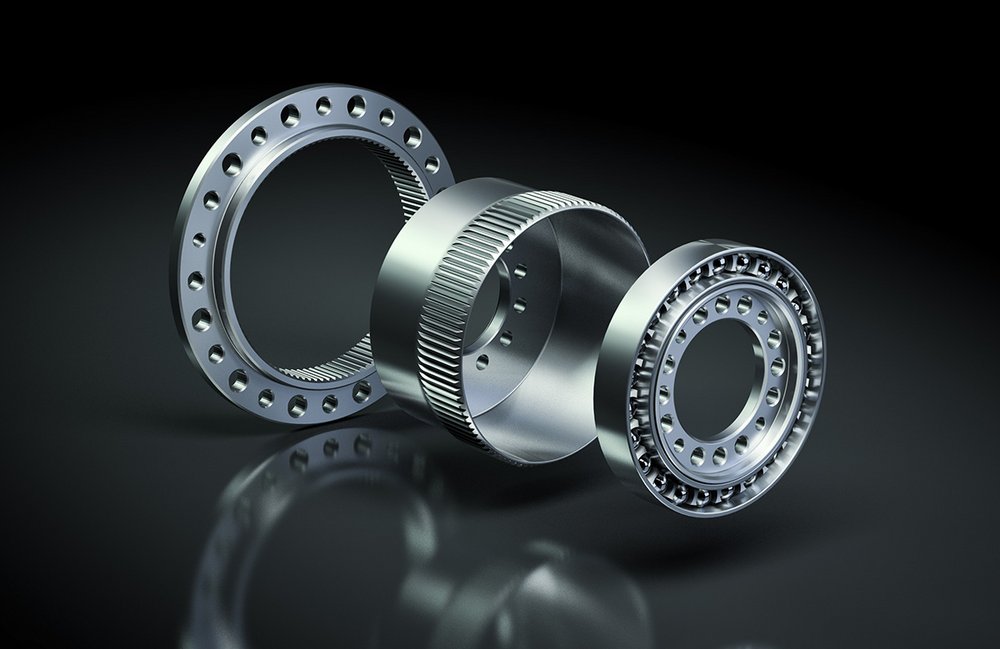
High torque capacity
Because power is transmitted over a wide gear mesh range, Harmonic Drive® Gears can transmit higher torques than conventional gears.
High reduction ratios in one stage
With only three components, gear ratios from 30:1 to 320:1 are achieved in one stage.
High efficiencies
Efficiencies of up to 85% are achieved in nominal operation. Harmonic Drive® Gears are not self-locking and do not exhibit stick-slip behaviour.

High torsional stiffness
Harmonic Drive® Gears have high torsional stiffness with a nearly linear characteristic over the entire torque range.
Central hollow shaft
Harmonic Drive® Gears offer the option of a central hollow shaft. Cables, shafts, laser beams etc. can be easily routed through the hollow shaft.
High reliability and long life
Harmonic Drive® Gears achieve much higher MTBF values than other gear types.
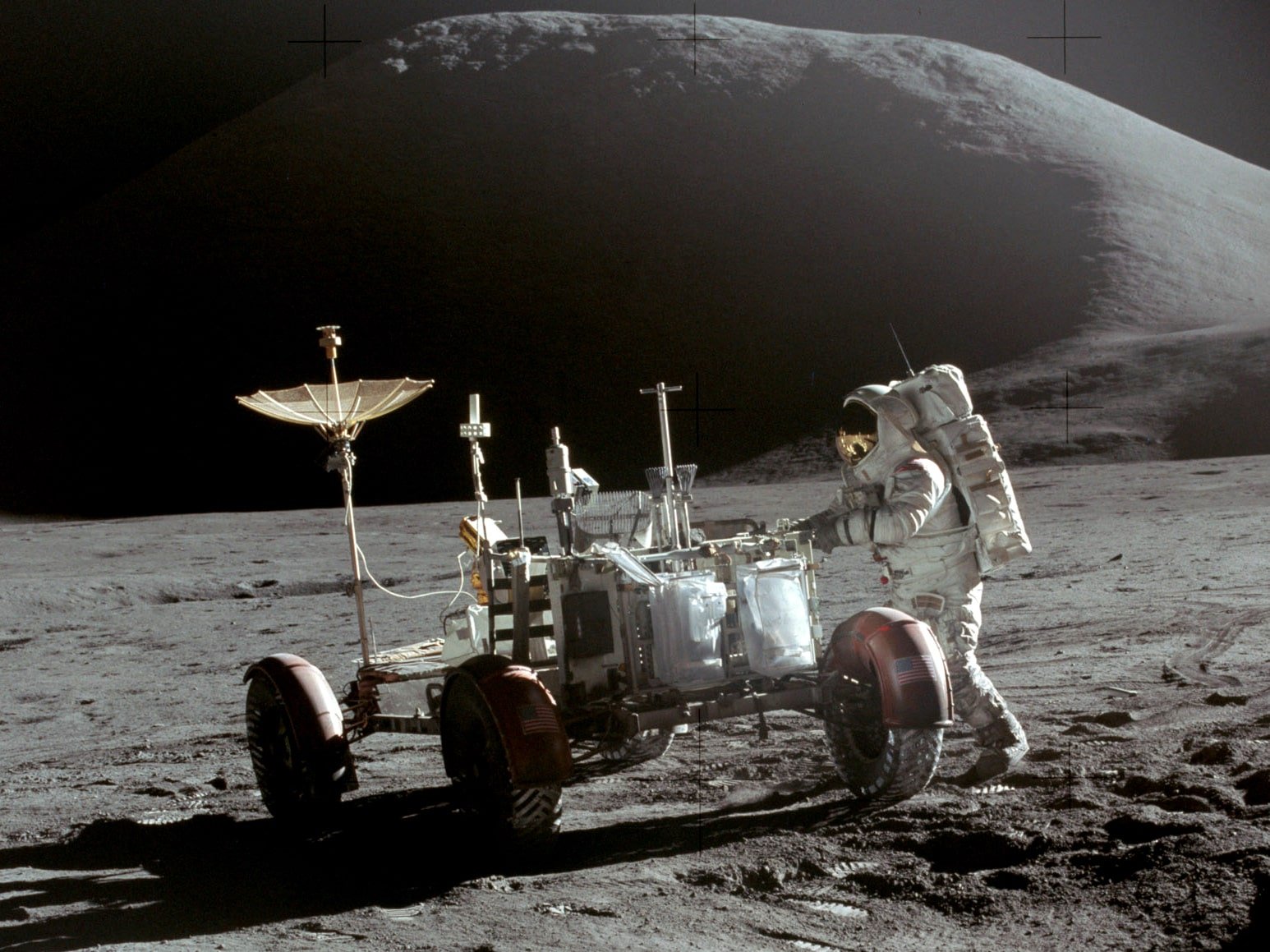
Mission Apollo 15 – Harmonic Drive® on the Moon
The year is 1971. On 26 July, Apollo 15 sets off for the moon from the Kennedy Space Center in Florida.
View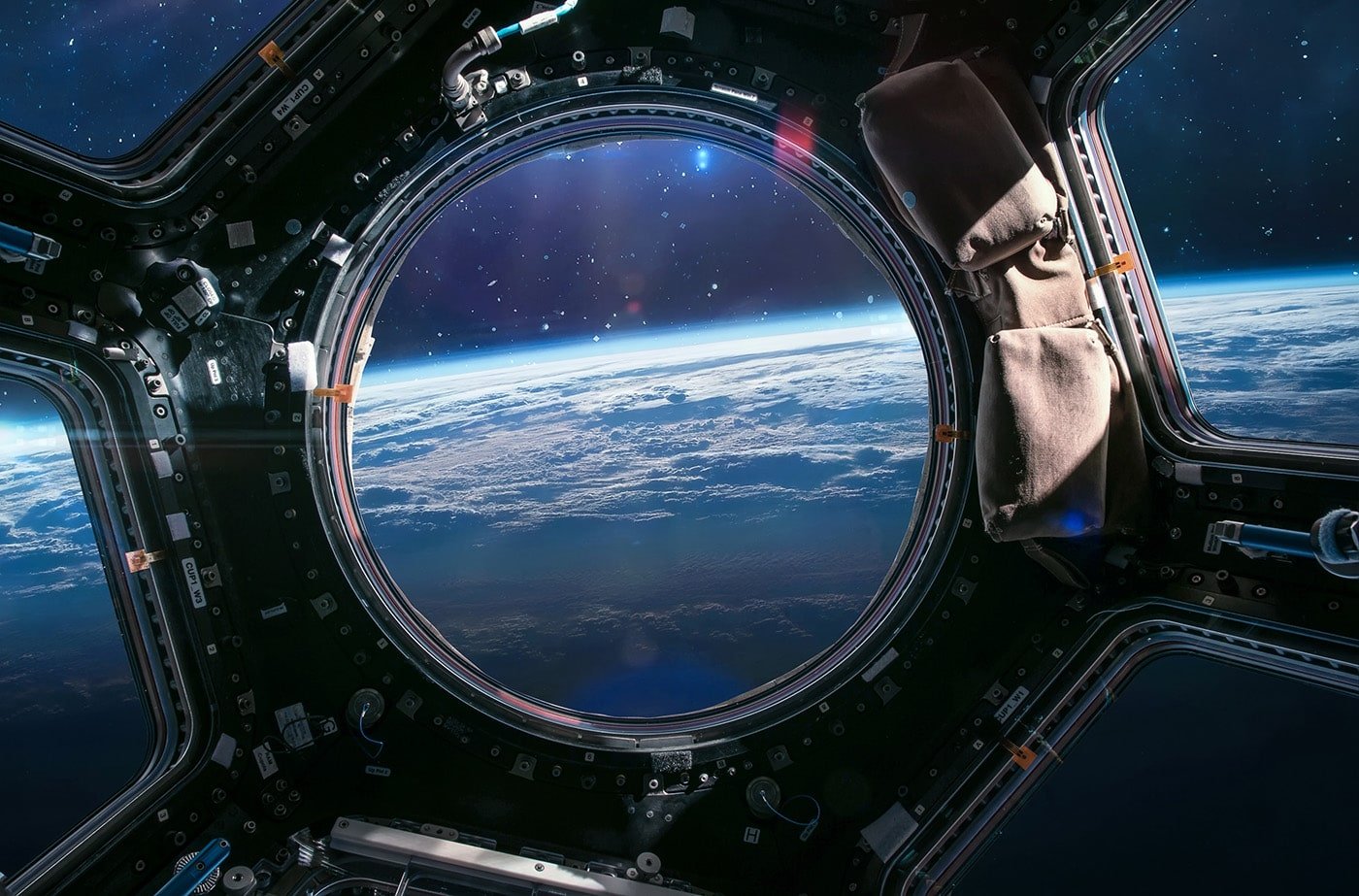
Around the globe with the ISS – Research at 400 kilometres altitude
In these applications on the International Space Station, Harmonic Drive® products ensure reliable operation.
View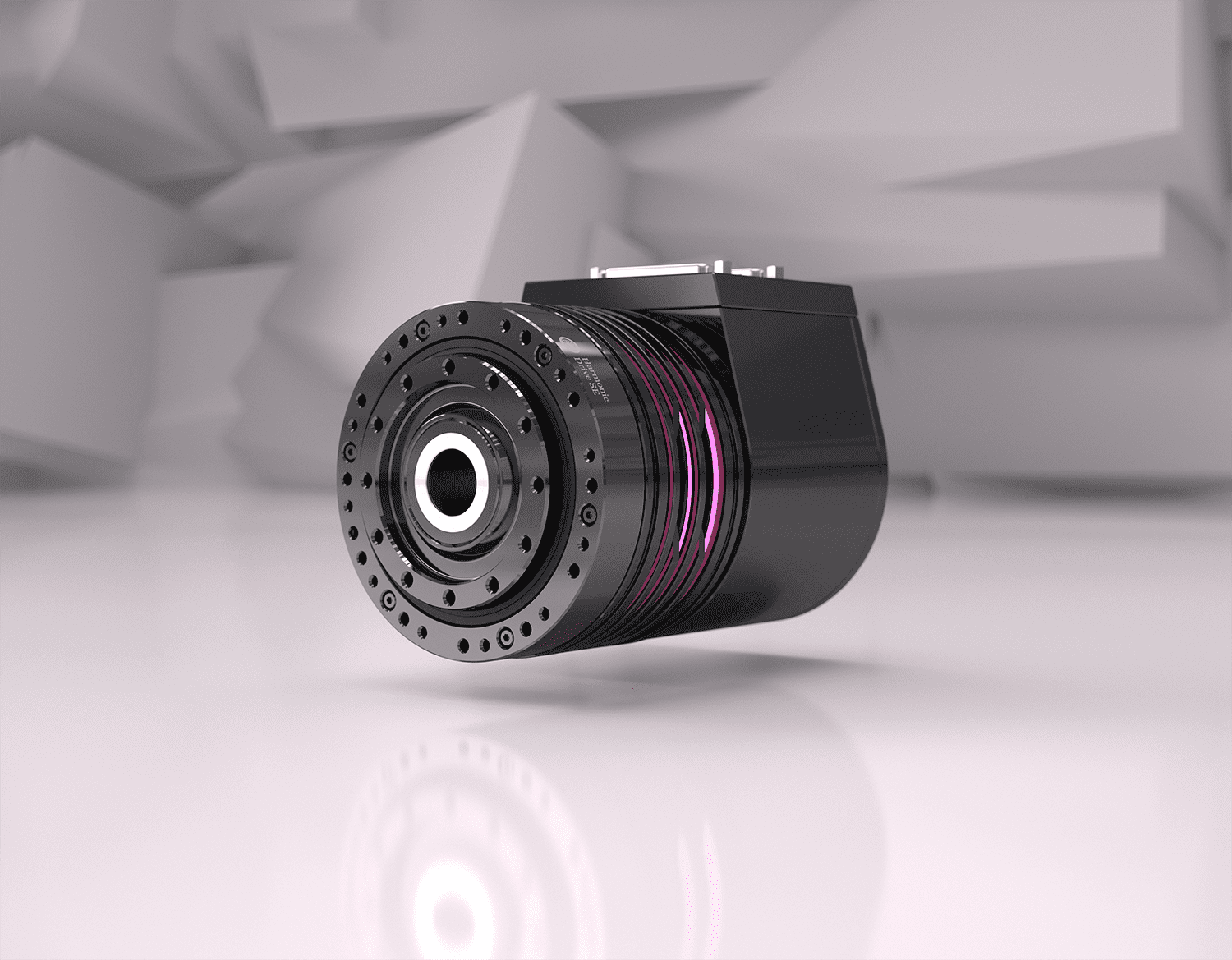
Smart System IHD: Pioneering drive technology
The need for compactness and intelligence is growing – especially in industrial and mobile drive technology.
View